Week one: An introduction to 3D printed design
by Nicole Swengley
In the first of three articles design writer, Nicole Swengley, explores the brave new world of 3D printed design.
The cutting-edge technology known as 3D printing is likely to shake up the collectables market as radically as it will re-shape our lifestyles. “We are at a tipping point in history where profound and radical changes in how we make things will revolutionise our lives,” says New York gallerist, Murray Moss, who curated the V&A’s show of 3D printed objects during London Design Festival last month.
This new technique belongs to a group of rapid-manufacturing technologies known as Additive Manufacturing. They all employ software packages to translate designs created as computer files into objects that are ‘printed’, three-dimensionally, by a machine. Products – from furniture to lighting, jewellery to shoes – are built up, layer by layer, and fabricated as complete units with no assembly required.
The technology embraces various techniques. Some, like 3D printing, use computer-controlled glue-guns to build up objects from fine layers of epoxy. Others employ infra-red lasers to create a solid form from a liquid such as resin (stereolithography) or from layers of fine powder ranging from nylon to titanium (selective laser sintering).
Unlike conventional manufacturing, which requires individual production moulds and tooling, 3D printers respond to computer programmes so it’s no more expensive or laborious to create 100 different objects than 100 identical ones. “It opens up completely new opportunities,” says designer Assa Ashuach whose Fly, Ai and Omi lights are available from Rabih Hage Gallery. “It allows me to make impossible objects that couldn’t be made in any other way,” says British designer, Michael Eden, whose latest 3D-printed vessels are unveiled by Adrian Sassoon at this month’s Pavilion of Art & Design show in London (12-16 October).
“You have complete freedom in terms of form and don’t have to consider how a design will be made,” adds Eden. “For younger designers, though, the technology still needs to go hand-in-hand with an understanding of materials and processes.” Indeed London’s Royal College of Art, which has its own rapid prototyping centre, encourages students to do just that while offering digital design, prototyping and manufacturing services to small businesses and individual designers in London. Facilities at Metropolitan Works’ Digital Manufacturing Centre at London’s Metropolitan University are also available to non-students. “This is a new industrial revolution and we’ve a long way to go,” enthuses Eden.
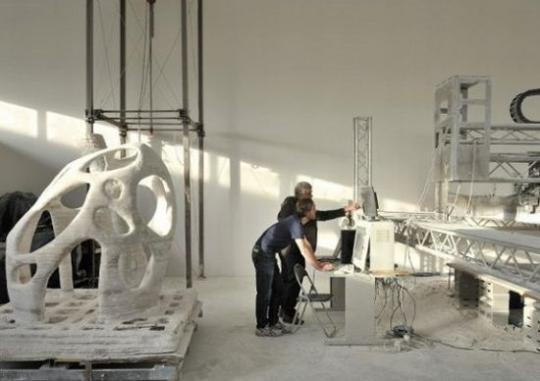
Designer Enrico Dini in studio